Mrs. Niveditha A S
Faculty – FD FDDI Chennai
Footwear Design & Development Institute(FDDI) was established in 1986, under the aegis of the Ministry of Commerce & Industry, Govt. of India. FDDI is playing a key role in imparting education, and facilitating the Indian industry by bridging the skill gap in the areas of Footwear, Leather Accessory & lifestyle product.
FDDI is a premier academic and training institution dedicated to the development and growth of the Footwear & Products, Leather Products, Retail and Fashion Merchandise and Fashion Design sectors. It has world class Infrastructure & Facilities created across the functional domain to ensure international standards of higher education, training & delivery for Footwear, Leather products, Retail and Allied Industries – 360° interventions under one umbrella. They have established an inhouse inhouse 3D printing services in Chennai facility of FDDI centre with an Industrial 3D printer at their lab to work on the development and innovation in Footwear industry.
“Stratasys Multi-color & Multi-material J55 prime 3D printer brings design imagination into reality. It gives us the ability to dress the shoe in a 360-degree design, which creates new opportunities in the Footwear and Fashion design.”
Mrs. Niveditha A S,
Faculty – FD
FDDI Chennai
In-House Stratasys J55 3D Printer.
Revolutionizing Sneaker Design: Full-Color Prototypes in Just Hours
Design prototyping is a crucial stage in sneaker design, enabling designers to test the functionality of their designs before sending them for production. FDDI utilized the Stratasys 3D Printer models, J55, based on polyjet technology to create Multicolor shoe prototypes. These prototypes showcase a variety of visual and geometric textures, representing the available materials for achieving a full-color model.
Traditional shoe model making involves complex, time-consuming, and expensive processes with multiple paint layers. It is also prone to errors, especially in flexible or soft areas. Achieving the desired color, texture, and detail on the entire 3D geometry of a shoe through traditional methods is challenging and costly. Maintaining accuracy in position, color, and tone is essential to ensure an excellent model evaluation and make informed design decisions.
One of the most remarkable advantages of using Single-step Polyjet 3D printing machine for footwear prototypes is the ability to achieve full-color models in just a few hours. This rapid turnaround time allows designers to iterate and fine- tune their designs much more efficiently. Previously, traditional methods required weeks to complete a single prototype, leading to prolonged development cycles and delayed decision-making.
Furthermore, the accuracy and precision of Polyjet 3D printing ensure that every detail, color, and texture of the shoe’s geometry is faithfully replicated in the prototype. This level of accuracy is challenging to attain through traditional means, where errors and inconsistencies may occur, hampering the evaluation process and leading to suboptimal design decisions. Moreover, available of wide range of 3D printing materials on this resin 3D Printer enables designers to explore a wide range of materials and textures, enhancing the creative possibilities for sneaker design.
“There’s lot of give and take in shoe design and the ability to quickly change a concept is key ”
Mr. Selvaraj,
Jr.Faculty SFDP
FDDI Chennai
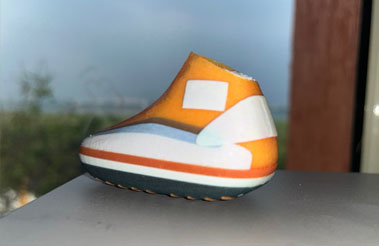
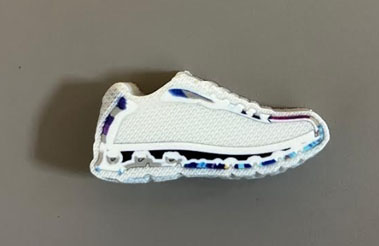
Prototype of Full color models of shoe concept, 3D printed in Stratasys J55 machine
Publication Date : March, 2023