Composite Tooling
Cost Effective Tooling in Days
3D print cost-effective, high-temperature, custom tools in days — instead of the weeks or months required for traditional tooling processes. Whether your application requires reusable layup mold tooling or sacrificial tooling for complex, trapped-tool geometries, FDM simplifies the fabrication of composite parts while provided unparalleled design freedom.
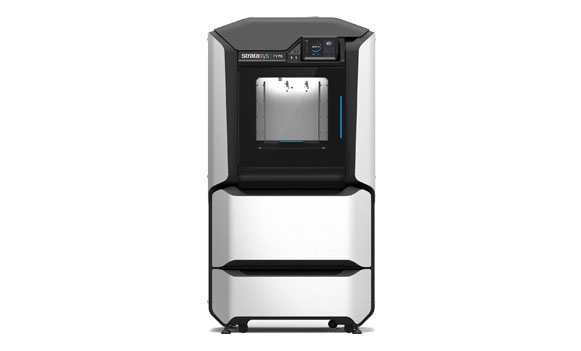
Composite Mold Tools in a Fraction of the Time
3D printed composite tooling using FDM technology offers the fastest, most cost-effective means of producing composite structures. FDM composite tools take only days to produce instead of weeks or months and avoid the high cost, touch-labor and long lead times of traditional tool fabrication.
We’re ready to solve the next generation of manufacturing obstacles. Are you?
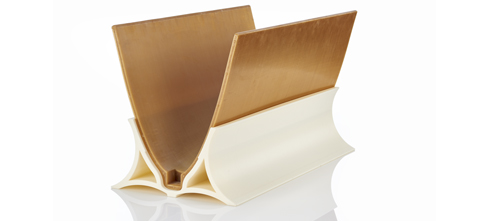
Reduce Cost & Lead Times
Build tools in days versus weeks or months for traditional tooling with more than 90% cost savings.
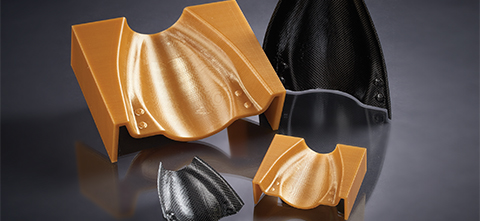
Produce Custom, Functional Designs
Tailor tool designs specifically to your application versus the “one size fits all” approach.
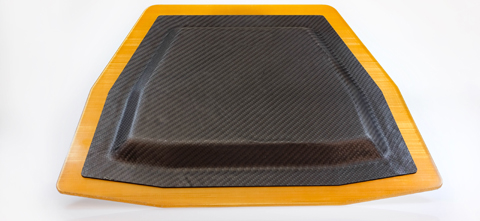
Respond Quickly To Fluctuation in Demand
Transition from pre-production parts to production in days with a digital inventory of tool designs ready for build.
Industries
Industries We Serve with 3D Printing & Advanced Manufacturing
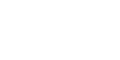
Rapid Prototyping
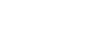
Functional Prototyping
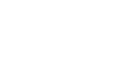
Tooling
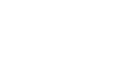
Injection Molding
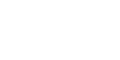
Jigs and Fixtures
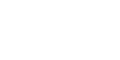
Production Parts
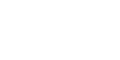
Rapid Prototyping
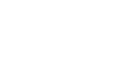
Tooling
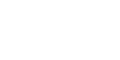
Jigs and Fixtures
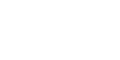
Production Parts
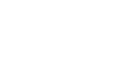
Spare Parts
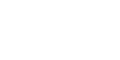
Rapid Prototyping
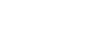
Functional Prototyping
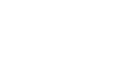
Concept/ Injection Modeling
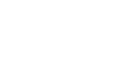
Orthodontic Models
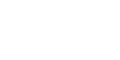
Cast Partial Frames
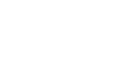
Implant Models
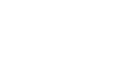
Surgical Guides
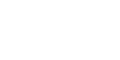
Research
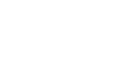
Preclinical Testing
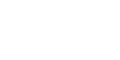
Clinical Training Models
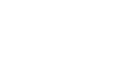
Medical Manufacturing
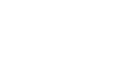
Surgical Planning Models
Featured Case Studies
IDEC and Wehl – EN FDM Case Study
Aerospace Case Study: IDEC is a leading Spanish provider of composite solutions for the aerospace industry, servicing its customers’ design and manufacturing needs. With the help of the advanced manufacturing service bureau, Wehl & Partner, the company embarked on a project to increase its competitiveness by reducing the time, cost, and material waste of traditional composite molding.
