Digimat
Unlocking the power of materials
Materials are used everywhere across multiple industries, ranging from material suppliers through automotive and aerospace to electronics and medical applications. By leveraging materials usages at their full potential, Digimat enables material innovation, lightweight product designs and reduces waste materials to create a significant and sustainable impact.
Digimat is the state-of-the-art multiscale material modelling platform focusing on the micromechanical modelling of complex multiphase materials such as plastics, composites, metals, and elastomers, revealing how they perform at part and system levels. Digimat bridges the gap between materials, manufacturing processes, and structural part performance to design innovative high-performance products while minimising weight, cost and time-to-market.
Digimat solutions form a holistic system based on three pillars:
- Digital materials laboratory to virtually design and test materials
- Multiscale simulations to enrich FEA and connect materials, manufacturing and performances
- Additive manufacturing focusing on polymers and composites
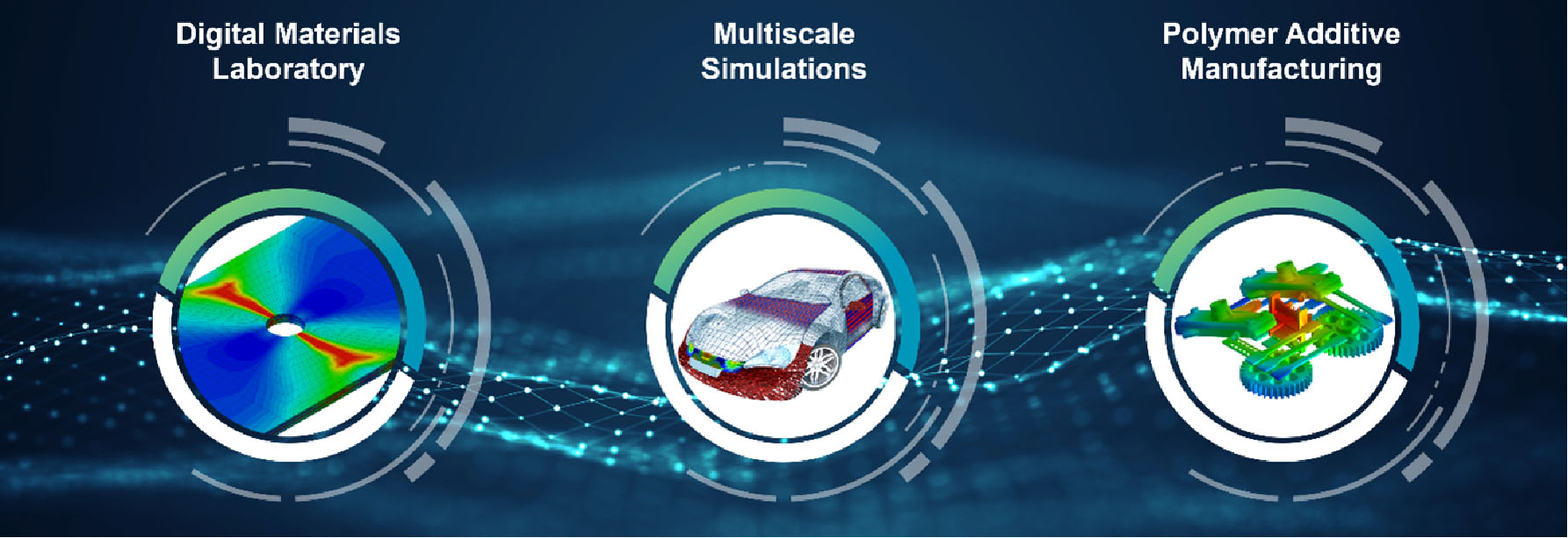
Digimat
e-Xstream engineering develops Digimat, a state-of-the-art multi-scale material modeling technology that helps speed up the development processes for plastic,composite and other heterogeneous materials and structures. Digimat is used by CAE engineers, specialists in manufacturing processes of composite materials, and materials scientists to accurately predict the nonlinear behavior of complex multi-phase composite materials and structures. Digimat, the award-winning software, is relied upon by major Material Suppliers, Tier1s and OEMS worldwide in various industries. It bridges the gap between manufacturing and structural performance. It helps multi-industries using plastics & composites.
Digimat’s applications follow three major strategies:
Material Engineering and Virtual Testing
The purpose of material engineering is to take a simulation approach for the identification of promising candidates for new composite materials thereby reducing the amount of experiments needed. This helps to save money and to reduce the time needed to develop new materials.
In research the approach allows to gain insight into and to understand mechanisms that dominate the macroscopic material properties but actually arise from its microscopic composition.
Process Simulation
Digimat provides process simulation solutions for the additive manufacturing of polymers. It helps process engineers to anticipate manufacturing issues and optimize part quality (ex: minimize warpage and residual stresses) by predicting the relative influence of the various process parameters. Digimat also has capabilities allowing to predict curing kinetic and its influence over the material and structural behavior of thermoset composite parts.
Structural Engineering
The purpose of structural engineering is to design full composite parts. The focus is on the part performance as it depends on the material characteristics and the manufacturing method and conditions that were used for the individual design.
Key to this challenge is a material model that correlates to experimental behavior as closely as possible. For this purpose a reverse engineering procedure is used that results in the parametrization of micro-mechanical models and their adaption to a set of anisotropic material measurements to meet the global composite performance best possible.
Such material models can now read locally different micro-structure information from various sources and convert them into a local material property. A fully coupled analysis results in a simulation model with individual material properties described for each integration point in the Finite Element analysis. Coupled analyses are state-of-the art for the modeling of composite parts and have proven to match experimental observation perfectly on many occasions.
The material modeling platform
e-Xstream’s team help engineers, managers and corporations optimize and improve their engineering processes by developing, implementing and customizing tools and solutions as well as consulting on critical projects:
Tools
A complete set of complementary interoperable software products focused on expert usage for material and/or structural engineering.
Solutions
Easy, process-centric, and user-friendly usage of Digimat technology from a fully integrated GUI guided environments for specific tasks (e.g. running coupled analyses for short fiber reinforced plastic parts with Digimat-RP).
eXpertise
Knowledge transfer from 15+ years of experience in micromechanical modeling. It includes a Digimat Users’ and Example Manual, as well as access to e-Xstream offers for services, support and trainings. Digimat, furthermore, offers online social platforms to share insights and get updated on recent activities and news.
Award-winning e-Xstream engineering


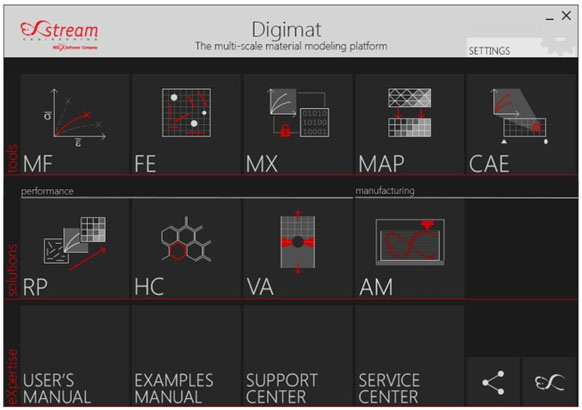
The technology is especially well suited for describing fiber reinforced composites:
- Short fiber reinforced plastics
- Long fiber thermoplastics
- Unidirectional composites
- Woven composites
A broad range of performances can realistically be predicted:
- Stiffness
- Failure
- Creep
- Fatigue
- Conductivity (thermal & electrical)
Nonlinear (per-phase) Material Models
- Linear (Thermo) Elasticity: Isotropic / Transversely isotropic / Orthotropic / Anisotropic
- Linear (Thermo)Viscoelasticity
- (Thermo) Elastoplasticity: J2 Plasticity and Isotropic hardening (Power / Exponential / Exponential laws) or Kinematic hardening (linear with restoration) for cyclic
- Pressure dependent elastoplasticity : Drucker- Prager
- Temperature and strain-rate dependent elastoplastic
- Elastoplasticity with Damage: Lemaître- Chaboche
- (Thermo) Elasto-Viscoplasticity: Norton / Power / Prandtl laws
- Viscoelasticity-Viscoplasticity
- Hyperelasticity (finite strain):
Neo-Hookean / Mooney-Rivlin / Ogden / Swanson / Storakers (compressible foams)
- Elasto-viscoplasticity (finite strain): Leonov-EGP
- Thermal & electrical conductivity: Ohm & Fourier
Failure Indicators
- Applied at micro and/or macro scale, or on pseudo-grains using the FPGF model (First Pseudo-Grain Failure model), including multilayer failure controls
- Failure models: Maximum stress and strain, Tsai-Hill 2D, 3D & 3D Transversely Isotropic, Azzi- Tsai-Hill 2D, Tsai-Wu 2D, 3D & 3D Transversely Isotropic, Hashin-Rotem 2D, Hashin 2D & 3D, SIFT, Christensen, User-defined
- Strain rate dependent failure criteria
- Failure criteria on Leonov-EGP & hyperelastic material models
Progressive Failure
- Failure: Hashin 2D / Hashin 3D / Hashin-Rotem 2D/ Multicomponent 2D
- Damage: Matzenmiller / Lubliner / Taylor (MLT) / Individual damage evolution functions
- Stabilization control using viscous regularization
Microstructure Morphology
- Multiple reinforcement phases
- Multi-layer microstructure
- Ellipsoidal reinforcements (fillers, fibers, platelets)
- Aspect ratio distribution
- General orientation (fixed, random, 2nd order orientation tensor)
- Void inclusions
- Coated inclusions with relative or absolute thickness
- Deformable, quasi-rigid or rigid inclusions
- Clustering
Homogenization Methods
- Mori-Tanaka
- Interpolative double inclusion
- 1st and 2nd order homogenization schemes
- Multi-step, multi-level homogenization methods
Fatigue
- Pseudo-grain based fatigue model specifically for short fiber reinforced plastics
- Matrix damage based fatigue model for unidirectional composites Pseudo-grain based fatigue model specifically
Loading
- Monotonic, cyclic or user-defined history loading
- Multi-axial stress or strain, General 2D & 3D, Harmonic
- Mechanical and thermo-mechanical
- Prediction of thermal & electrical conductivities
Further functionalities:
- Prediction of orthotropic engineering constants
- User defined outputs
- Interoperability with Digimat-FE and Digimat-MX
- Handling of encrypted material files
Digimat-FE
Digimat-FE is the tool performing computational homogenization, starting at microscopic scale in order to gain an in-depth view into the composite material by the direct investigation of Representative Volume Elements (RVEs). Digimat-FE can act as a stochastic generator of highly realistic RVEs covering a large variety of materials: plastics, rubbers, metals, ceramics, nano-filled materials. It also allows importing
microstructure from geometry files (e.g. STL files) or 3D image files (e.g. RAW file), or to manually import single inclusion geometry and position them within the RVE.
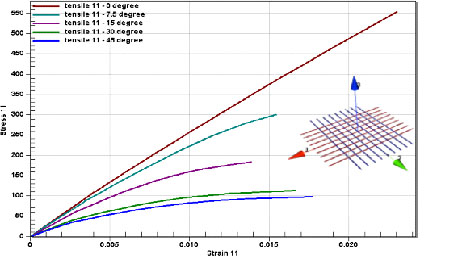
Based on material input and the microstructure definition, a finite element model is built and submitted to analysis. The results of the FE analysis are post-processed by using probabilistic distribution functions that give detailed insight into the RVE. Mean homogenized values are computed and can be used in subsequent FE analysis on the structural part level.
Digimat-FE allows to solve the problem at-hand over the RVE using internal Finite Element of FFT/spectral solvers, or to export corresponding finite element models.
End-to-end solution
A complete end-to-end solution has been implemented in Digimat. It allows performing all the different steps needed to obtain a complete FE analysis – starting from the material data. For instance, the steps followed to model woven composites are:
- Extraction of the material data from the datasheet
- Mean-field homogenization of the yarns
- Generation of a geometry of a unit cell
- Generation of a RVE
- Voxelisation
- FE model definition and application of periodic boundary conditions
- Solving the FE analysis
- Post-processing the outputs of the FE analysis
Latest Capabilities
- New microstructures
- Foams: open and closed cells (random or periodic
- Polycrystalline materials
- Lattices
- Imported from STL geometry or RAW images files
- User defined failure indicator
- Custom weave pattern for woven 3D
Main Capabilities
- Definition of composite constituents
- Inclusion shapes (Spheroid, Platelet, Ellipsoid, Cylinder, Curvy fibers, User defined, )
- Material models (Elastic, (Thermo) Elastic, (Thermo) Elastoplastic, Viscoelastic, )
- Inter-operability with Digimat-MF and Digimat-MX
Embedded solver
- Digimat-FE solvers for end-to-end solution
- Finite element solver with CPU based
- Spectral solver with CPU & GPU based
- FE analysis can be started & monitored from within Digimat- FE
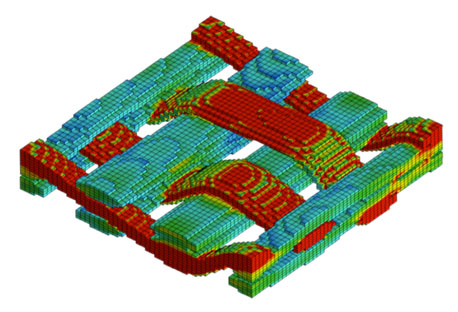
Voxel based solution for a woven 2.5D composite material computed in Digimat-FE
Microstructure Definition
- Predefined phase types: matrix, inclusion, continuous fiber, void, yarn, strand, grain
- Microstructure morphology definition: Volume /Mass fraction
- Multiple inclusion shapes
- General orientation definition (fixed, random, 2nd order orientation tensor, from EBSD/ODF data for polycrystalline materials)
- Fiber length or grain size with access to size distribution
- Coating
- Inclusion / Matrix debonding
- Multi-layer microstructure
- Predefined microstructures: generic, fabrics, lattices, foams, polycrystalline metals, cemented
- Imported from STL geometry or 3D RAW image
RVE Generation
- RVE microstructure generation with real-time preview & animation process
- Random positioning, maximum packing or random perturbation algorithms
- 3D & 2D RVEs
- Unit cell generation
FE Meshing
- Voxel and conforming internal mesher available for FE/ Solver
- Grid generation for FFT/Spectral solver
- Export finite element models to : Marc, Abaqus/ Standard, Ansys and LS-Dyna.
- RVE meshing embedded beam elements, straight or curved