Marc
MSC Marc is a nonlinear finite elements analysis software used to simulate behavior of complex materials and interaction under large deformations and strains. It can also simulate multi-physics scenarios across structural, thermal, piezoelectric, electrostatic, magnetostatic, and electromagnetic behaviors. It uses automatic two-dimensional and three-dimensional remeshing to analyze structures undergoing large distortions, and crack propagation. Major categories of non-linearity, namely geometric, material and boundary condition nonlinearities that involve large deformations and strains, contact interaction, damage, fracture and failurecan be analysed.

History
Marc was the first commercial nonlinear finite element software developed by Marc Analysis Research Corporation founded in 1971 by Dr. Pedro Marcel. It was acquired in 1999 by MSC Software Corporation. Mentat is the dedicated pre- and post-processor used to support Marc.
Mechanical Simulations Scenarios
- Linear statics
- Linear dynamics
- Nonlinear statics
- Nonlinear dynamics
- Buckling
- Heat transfer
- Diffusion
- Electromagnetics
- Electrostatics
- Magnetostatics
Coupled Physical Phenomena
- Themomechnical
- Electrical-Thermal-Mechanical
- Piezoelectric
- Induction heating
- Thermal-Electrical (Joule heating)
- Magnetodynamic-Thermal
- Magnetostatic-Structural
- Magnetostatic-Thermal
Marc can be used to model materials like:
- Metals, below and above the yield point
- Composite materials
- Gaskets
- Thermomechanical shape memory alloys
- Soils
- Powder metals
- Concrete
- Elastomers
- Plastics
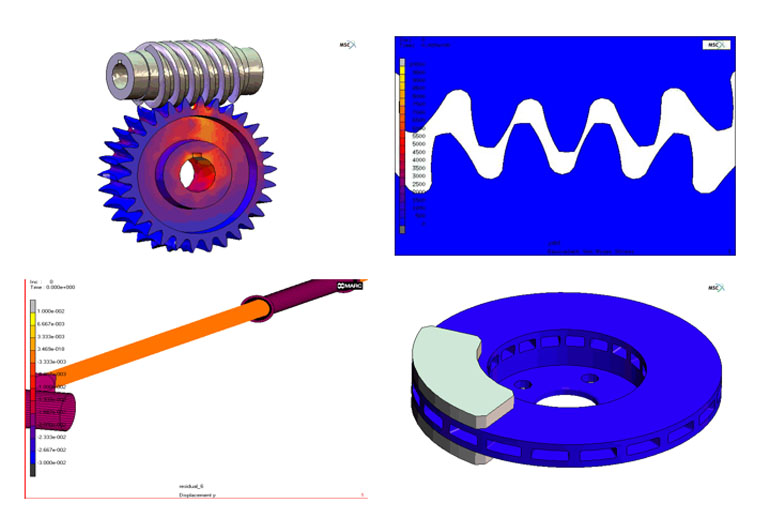
Implicit Non linear Analysis
- Coupled solutions of nonlinear structural, thermal, electromagnetics
- Advanced heat transfer analysis
- Special purpose material models including Shape Memory Alloy and Solder models
- Motion and suspension analysis powered by Adams
- Advanced damage and fatigue analysis of metals and composite structures
- Crack initiation and propagation under realistic load conditions
Materials in your designs
- Metals undergoing plasticity, elastomers, plastics, composites, powder metals, shape memory alloys
Large Deformation
- Buckling, snap through (bottle caps, paper clip, balloon inflation)
- Folding (seals)
Loads
- Interaction between structures (contact)
- Components sliding with respect to each other
- Loads changing with deformation
Multi-physics
- Temperature affecting structural performance
- Electromagnetic fields influencing performance
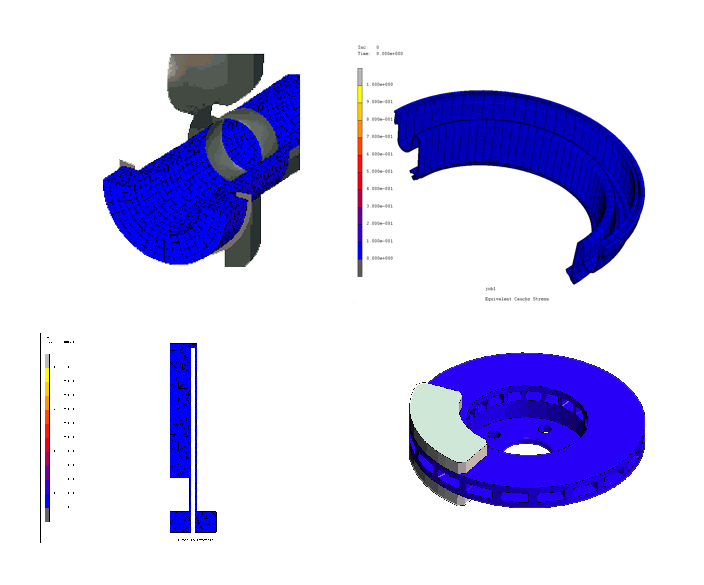
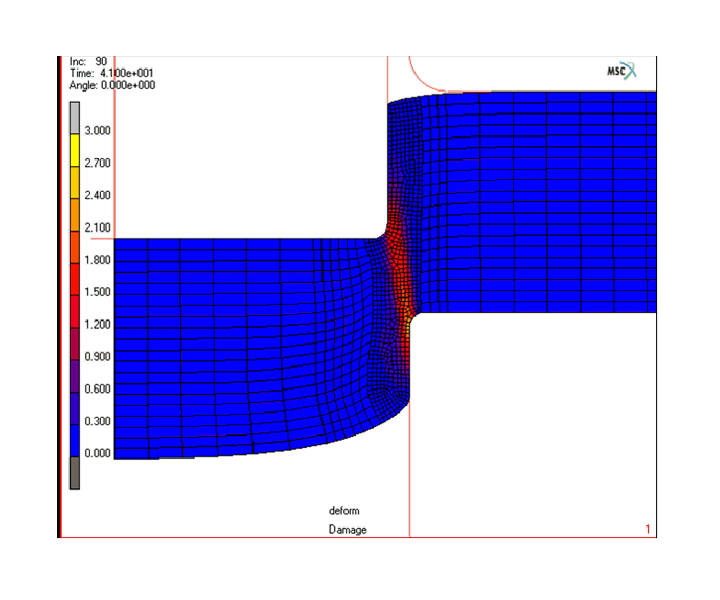
Sheet-Metal Shearing
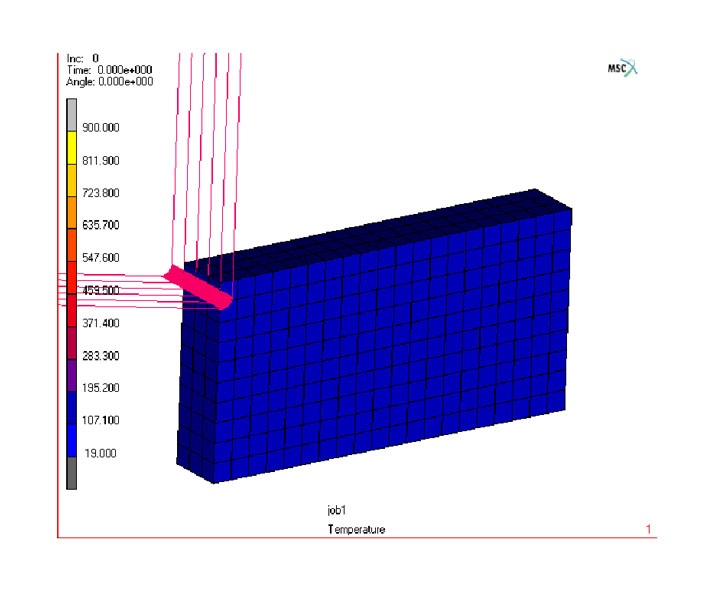
3D Cutting
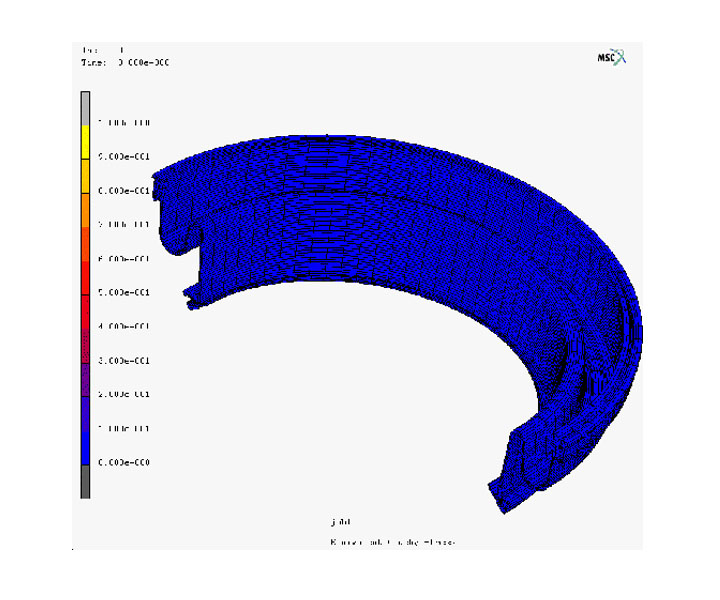
Cauchy Stress
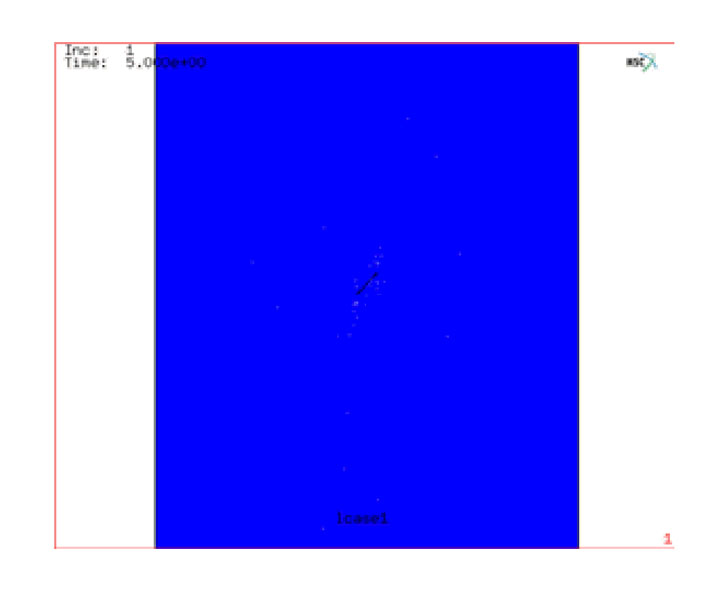