Simufact
Why Simufact Solutions?
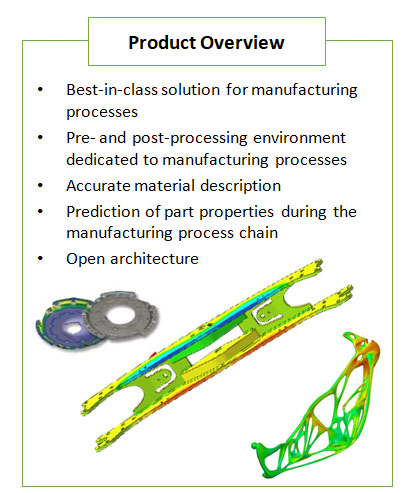
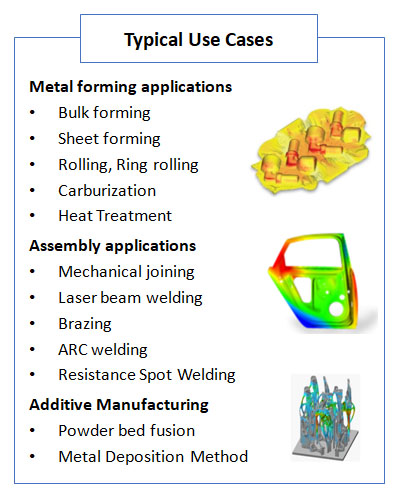
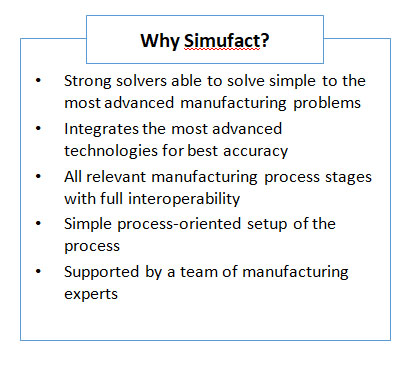
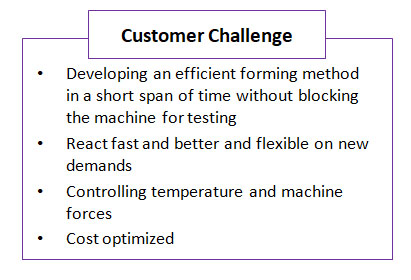
MODULES OF SIMUFACT
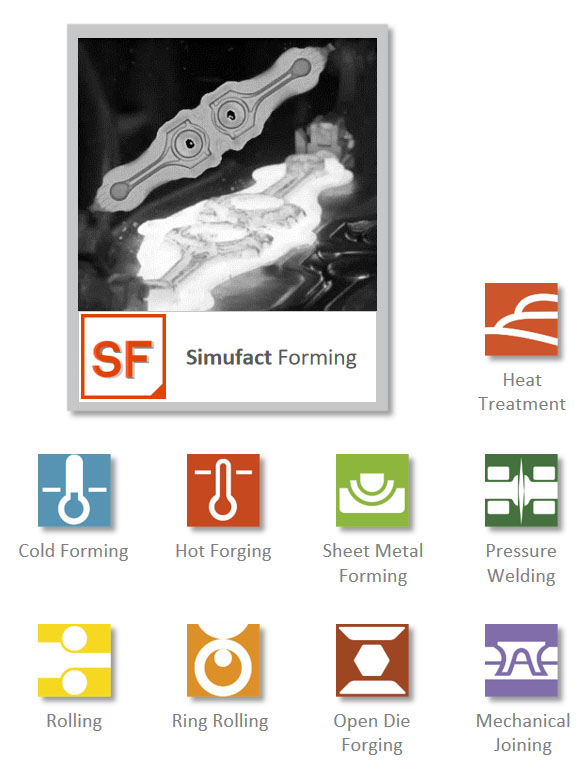
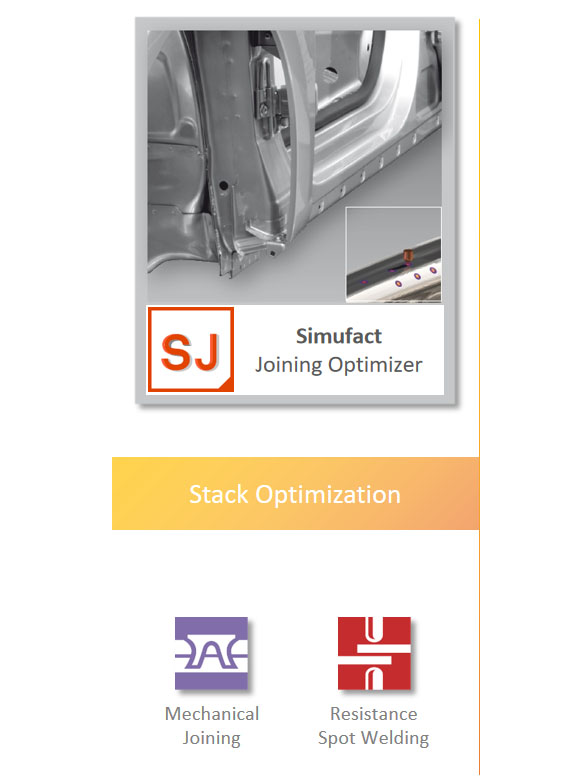
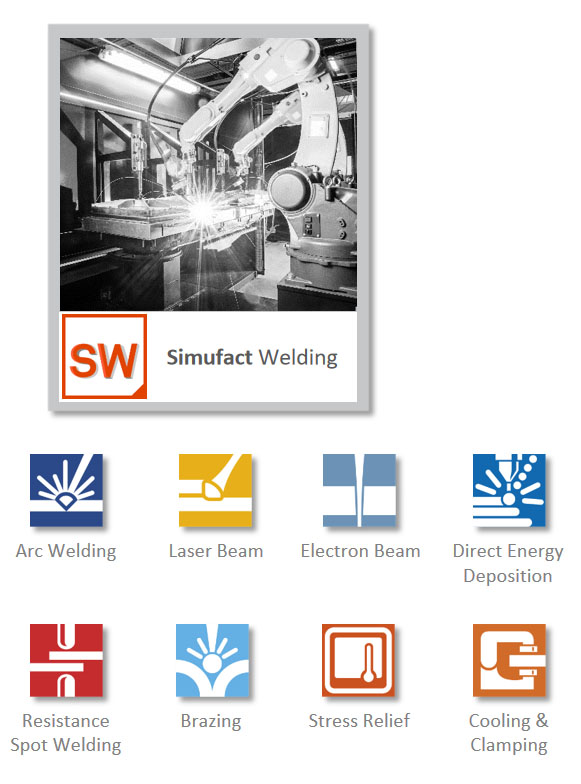
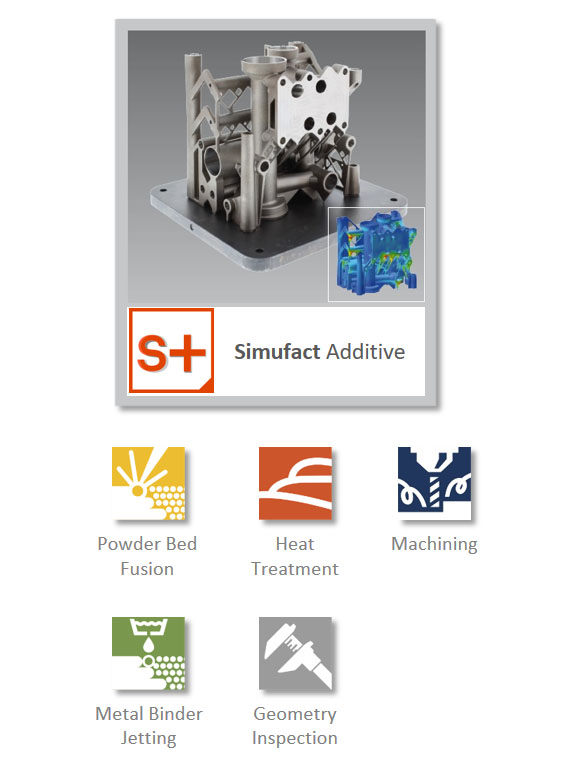
Specialised forming simulation software for virtual testing and process design for component optimisation
- Simufact software solutions allow you to simulate a wide range of forming, joining processes, as well as metal-based additive manufacturing processes to optimise manufacturing processes, reduce costs and time-to-market, while improving product quality.
- The Simufact software solutions are divided into three product lines that have been developed for the specific requirements of each individual processes: Simufact Forming, Simufact Welding and Simufact Additive.
- Simufact Forming is an established software solution for the simulation of metal forming manufacturing processes. The software covers all essential areas of forming technology: forging, cold forming, sheet metal forming, all major incremental processes and mechanical joining. Simufact Forming provides support in microstructure simulation, calculation of die load, material flow and prediction of material properties in the course of conventional and inductive heat treatment. Furthermore, thermo-mechanical joining methods of pressure welding are also supported.
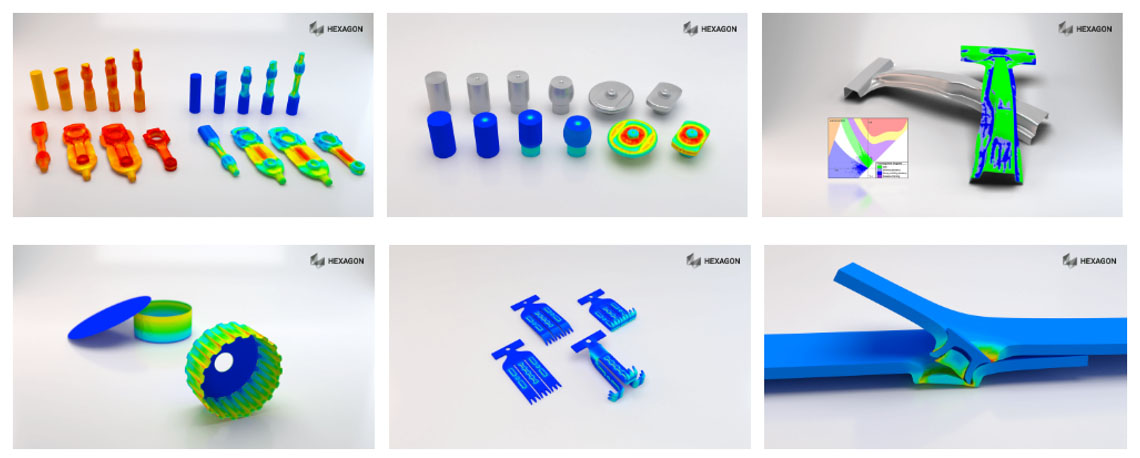
Specialised forming simulation software for virtual testing and process design for component optimization
The user interface of Simufact Forming was developed to be simple, intuitive and process-oriented. This makes Simufact Forming a design tool for the tool and process developer that supports and simplifies the user’s daily work. With just a few mouse clicks, all standard forming processes can be set up and evaluated

Cold Forming
Forming processes conducted significantly below the recrystallization temperature of the material. These processes include typical upsetting and extrusion processes (e. g. to produce bolts, nuts and rivets).

Hot Forging
Forming processes conducted above the recrystallization temperature of the material. A typical process is hot forging, including closed die hot forging.

Sheet Metal Forming
Sheet metal forming includes: Drawing processes (e. g. deep drawing, reverse drawing, collaring, tapering and stretching), wall ironing, blanking, stamping and bending, fine blanking, coining, roll forming, and more

Rolling
Forming processes in which the material is formed between two or more rotating dies (rollers). Examples of rolling processes include; flat and profile rolling, spinning, flow forming and reduction rolling.

Ring Rolling
Special rolling method for the manufacturing of seamless rings with related sub-methods such as; radial ring rolling, radial-axial ring rolling and axial closed die rolling.

Mechanical Joining
Forming processes that cause a mechanical interlock between the pieces. Mechanical joining includes riveting methods such as; punch riveting, self-piercing riveting and blind riveting, as well as clinching technologies such pressure joining, clinching and toxing.

Pressure Welding
Pressure welding stands for a group of joining processes in which components are joined by heating and compression. Heat can be generated either via current (resistance welding) or by using friction (friction welding).

Resistance Spot Welding
Resistance Spot Welding is a pressure welding process during which the sheets are pressed together locally with the help of fitted copper electrode welding guns. The electrical current between the weld guns causes a heating and melting of an assembly.
APPLICATIONS
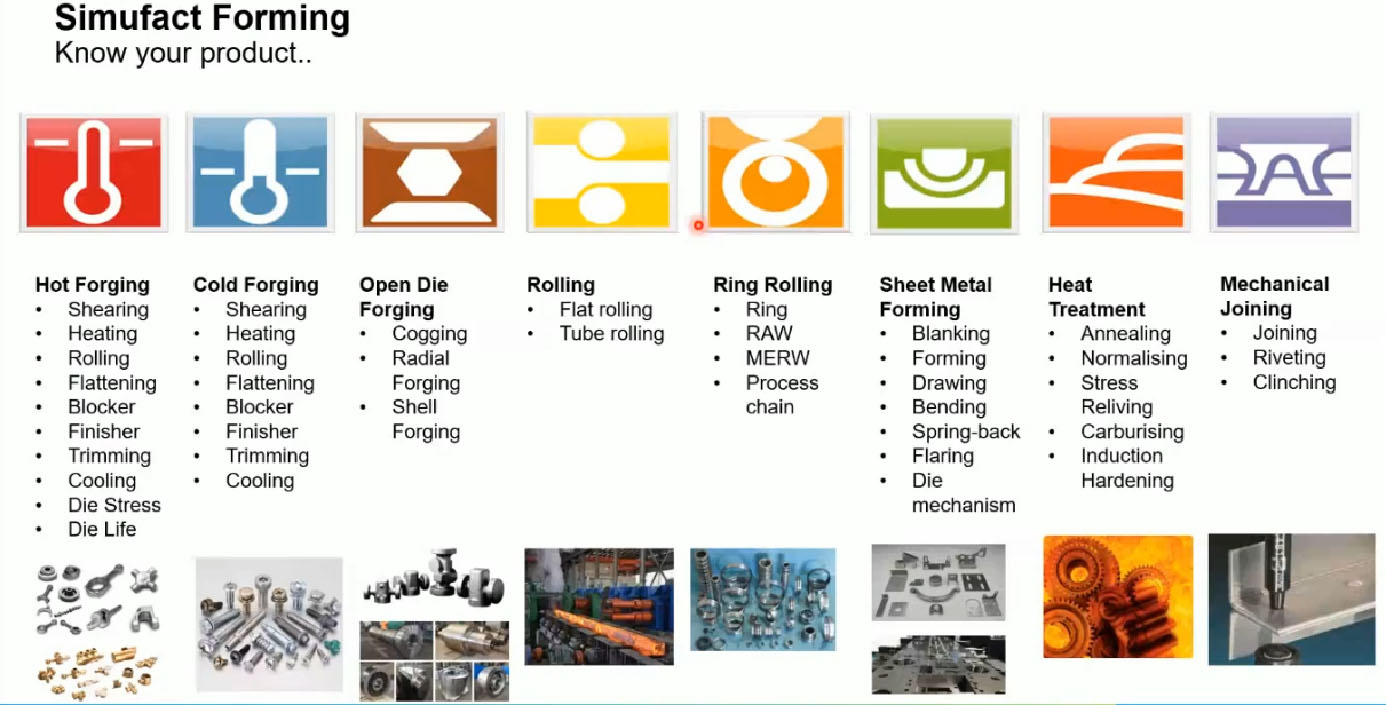
Special weld structure software for virtual tests and process design for the optimisation of assemblies
Simufact Welding is used for modelling and optimising a wide range of fusion and pressure welding processes, taking into account weld sequence and clamping. Processes such as arc welding, laser beam welding, electron beam welding, brazing, resistance spot welding as well as the generative manufacturing process ‘Direct Energy Deposition’ (DED or WAAM) can be modelled in Simufact Welding. Additionally, Simufact Welding can be used to model the heat treatment, different variants for cooling and unclamping as well as the mechanical load on welded structures.

Processes such as arc welding, laser beam welding, electron beam welding, brazing, resistance spot welding as well as the additive manufacturing process laser deposition welding (LMD or DED) can be modeled in Simufact Welding. In addition, Simufact Welding can be used to model the heat treatment, different variants of cooling and stress relieving as well as the mechanical load of the welded structures.
Special weld structure software for virtual tests and process design for the optimization of assemblies
- Welding is the most important procedure to create assemblies with high strength in an automated environment
- High-cost pressure in process design (labor, stock material, equipment, energy)
Lower time-to-market requirements for delivering new products
Low margins with commoditization of welded structures - Modern CAE tools are one part of the solution
> To optimize clamping fixtures and weld sequences
> To shift expensive physical tryout loops into simulation environment
> To achieve remarkable cost savings within short time periods
> To improve time-to-market performance - Customers gain benefits from our solution by
> Design with process optimization
> Increasing quality index
> Declining scrap and rework measures
> Material & energy savings
> Reducing down times & and set-up times
> Create additional resources for new business with existing assets
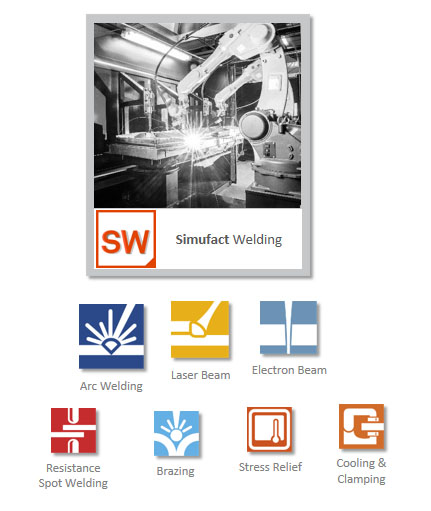
Special weld structure software for virtual tests and process design for the optimisation of assemblies
Your benefits with Simufact Welding
- Design and optimise your welding process:
> Determine the optimal weld sequence and parameters, as well as clamping and unclamping concepts, to minimise thermal distortions and residual stresses and ensure a robust welding process.
> Identify and eliminate potential welding defects, such as hot cracks.
> Investigate material behavior during welding, such as phase transformation - Simplicity – No expert knowledge required as the software solution is designed to be user-friendly, intuitive and process-oriented.
- Sustainability – Save material, time and money by replacing expensive and time-consuming physical tests with virtual tests.
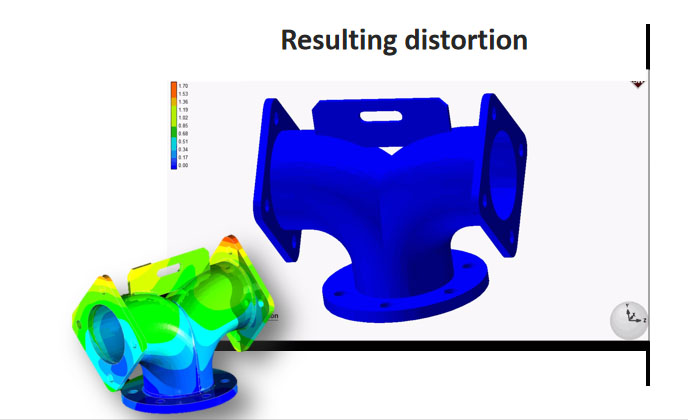
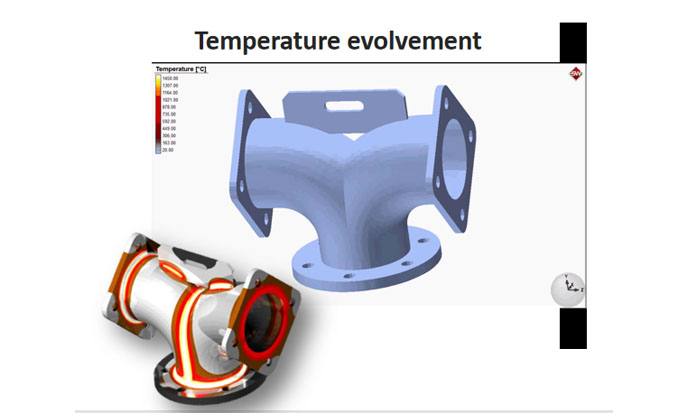
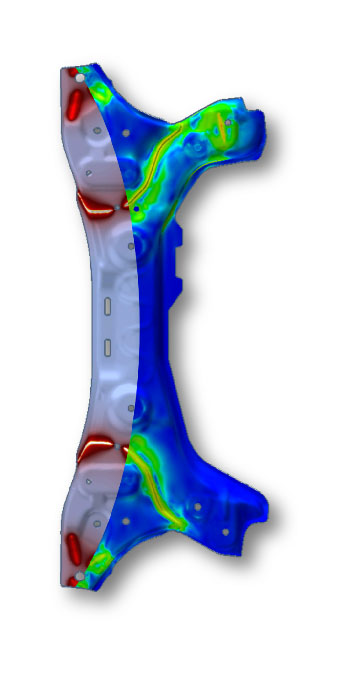
Special software for virtual testing and process design for optimisation of metal-based additive manufacturing
Simufact Additive is a scalable software solution for the simulation of metal-based additive manufacturing processes which focuses on powder bed melting (L-PDF) and metal binder jetting (MBJ) processes. Simufact Additive is a software solution designed to predict and compensate for distortion, residual stress and temperature distribution throughout the printing, heat treatment, cutting, hot isostatic pressing (HIP) as well as machining processes virtually before the part is manufactured by the 3D metal printer in reality.
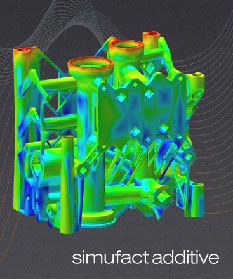
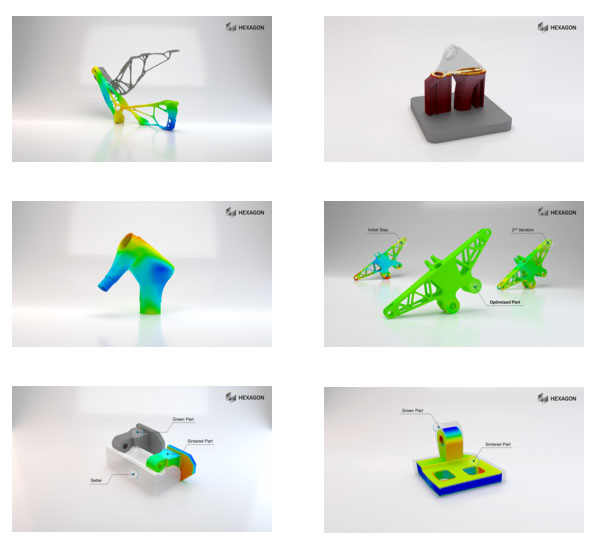
Special software for virtual testing and process design for optimisation of metal-based additive manufacturing
Simufact Additive – a New Software Generation
Leading build simulation software
- Intuitive, user-friendly, easy of Use
- Process-oriented
- Clean Surface
- Quickly productive
- Fast modeling
- Combining best technologies
- Process chain simulation
- Scalable solution
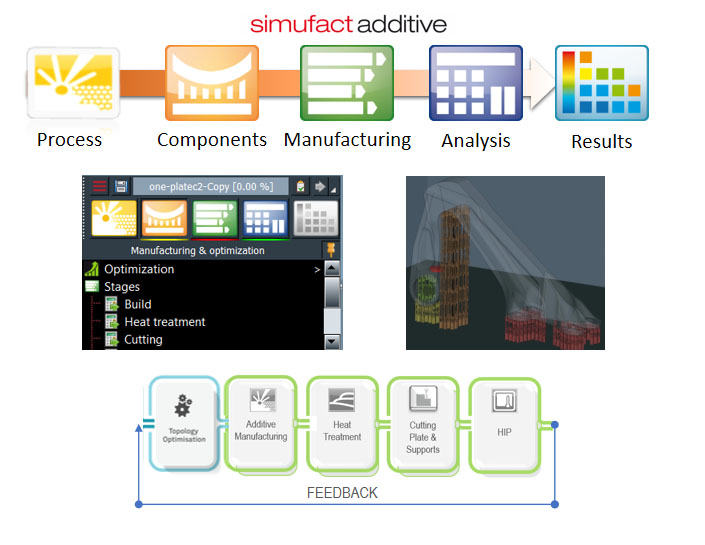
Special software for virtual testing and process design for optimisation of metal-based additive manufacturing
- Sustainability: Save material and money by replacing expensive physical tryouts with virtual tests
- User-friendly, intuitive and process orientated GUI
- Deepen your knowledge of the metal AM process
> Compensate distortion automatically to print the part as-designed
> Optimise the build-up orientation and the support structures
> Indicate criteria-based part failures, i.e. shrink lines - Estimate your costs for single parts and the entire printing job
Simulation of Power Bed Fusion Processes
Simufact Addictive covers the simulation of Power Bed Fusion Processes, e.g. know as,
- Selective Laser Melting (SLM)
- Direct Metal Laser Sintering (DMLS) – an EOS technology
- LaserCUSING – A concept laser technology
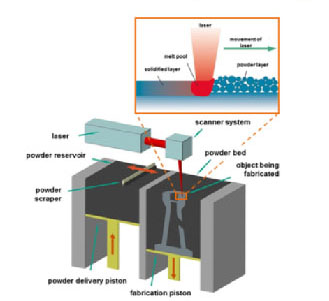
Special software for virtual testing and process design for optimisation of metal-based additive manufacturing
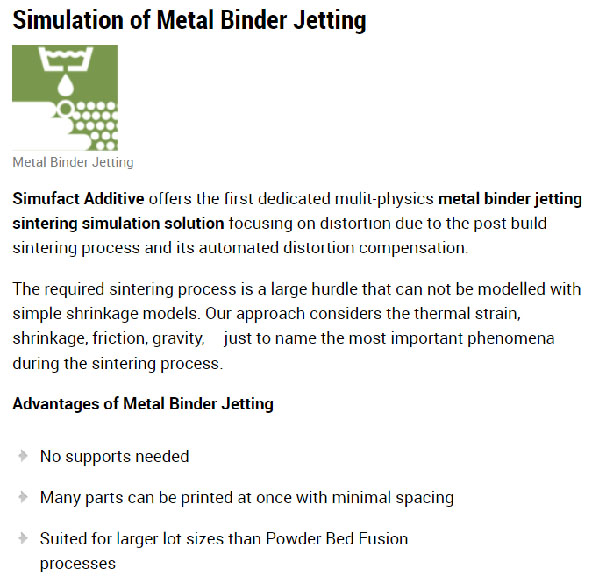
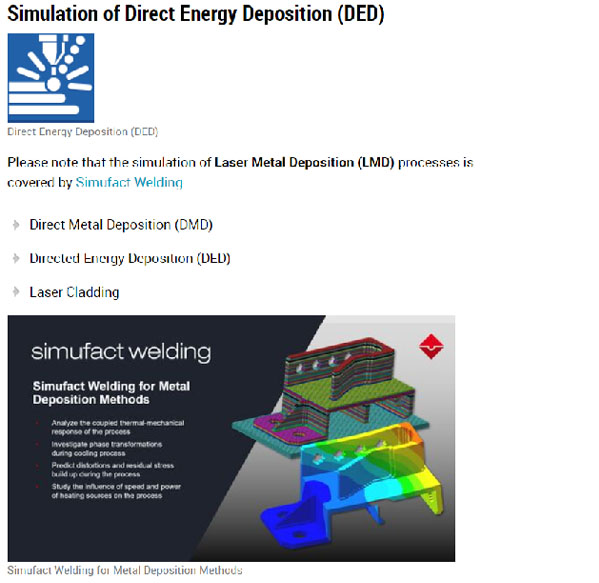