Binder Jet Technology
Enabling True Multi-Material 3D Printing
Introduction to Binder Jet 3D Printing
Binder Jetting is an additive manufacturing process that involves the selective deposition of a binding agent onto a powder bed. This 3D Printing technology is renowned for its ability to produce complex geometries, intricate details, and a wide range of materials. Unlike other 3D printing technologies that rely on melting or sintering materials, Binder Jet 3D Printing technology uses a binding agent to join powder particles, offering unique advantages. The promises of additive manufacturing are limitless: printing entire assemblies and organic shapes without design constraints, no tooling requirements or lead times, and fast, local production options.
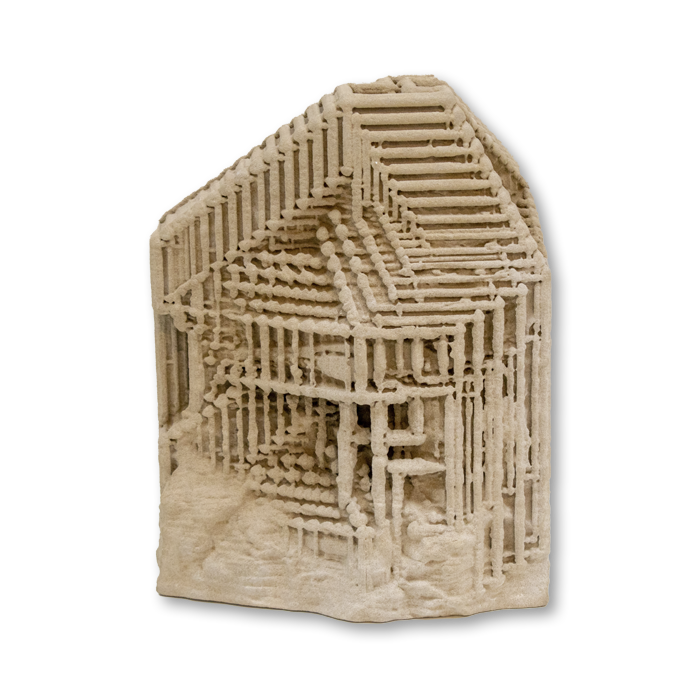
How Binder Jetting Works
Binder jetting 3D printing technology is based on two key elements: a powder and a binder. The powder can be a mineral, metal, ceramic, or another material you want to bond in powder form. The binder is a liquid, which acts as an adhesive between powder layers.
Preparation of the Powder Bed
A thin layer of powdered material (metal, sand, ceramics, or composites) is spread across the build platform using a roller or blade.
Deposition of the Binding Agent
An inkjet print head selectively deposits droplets of a liquid binding agent onto the powder bed, following the cross-sectional pattern of the object being printed.
Layer-by-Layer Construction
The process repeats layer by layer. Each new layer of powder is spread over the previous one, and the binding agent is deposited to bond the layers together. After each layer, the printed object is lowered on its build platform by the layer thickness. A new layer of powder is deposited, and the process repeats. Unbound powder remains in position surrounding the printed object.
Post-Processing
Once the entire object is printed, excess powder is removed. The printed part often undergoes additional processes such as curing, infiltration with a secondary material, or sintering to enhance strength and other properties.
Any print starts with a 3D model of the object or product, which can be included in a print job. The 3D Printing software, designed specifically for optimizing binder jet 3D printing enhances the user experience. Through its intuitive interface, the the 3D Printer design software provides full control over variables like layer height and print speed. Printed objects are self-supported and don’t require additional structures.
Advantages of Binder Jetting
Material Versatility
Binder Jetting supports a wide range of materials, including metals, ceramics, stone powder and polymers, thus enabling metal 3D Printing or ceramic 3D Printing This versatility makes it suitable for various applications across different industries. This multi-material 3D printer offers unparalleled flexibility, making it ideal for diverse applications across different industries. Multi-material 3D printing allows for the creation of complex parts with varying properties, further expanding the potential uses of this technology.
High Speed and Productivity
The binder jet 3D Printing process is relatively fast compared to other additive manufacturing technologies because it doesn’t require melting and solidifying materials. Multiple parts can be printed simultaneously, increasing productivity.
Cost-Effectiveness
Since Binder Jet 3D Printing process does not require high temperatures, energy consumption is lower. Additionally, the ability to reuse unbound 3D Printing materials powder reduces material waste, making it a cost-effective solution for prototyping and production. Our proprietary binder jetting technology now offers you the tools to harness its full potential, with a cost-efficient platform that goes above and beyond traditional production methods.
Complex Geometry and Fine Details
Binder Jet 3D printers can produce complex geometries and fine details with high precision. They are ideal for creating intricate patterns, internal structures, and customized designs. This capability is especially valuable in industries that require detailed and precise components, such as aerospace, electronics, healthcare etc. The technology allows for the creation of lightweight structures with internal channels and voids, which are difficult to achieve with traditional manufacturing methods. Additionally, the high resolution of Binder Jetting, whether using as ceramic 3D Printer or metal 3D printer, enables the production of parts with fine surface textures and minute features, meeting the stringent requirements of various high-performance applications.
We’re ready to solve the next generation of manufacturing obstacles. Are you?
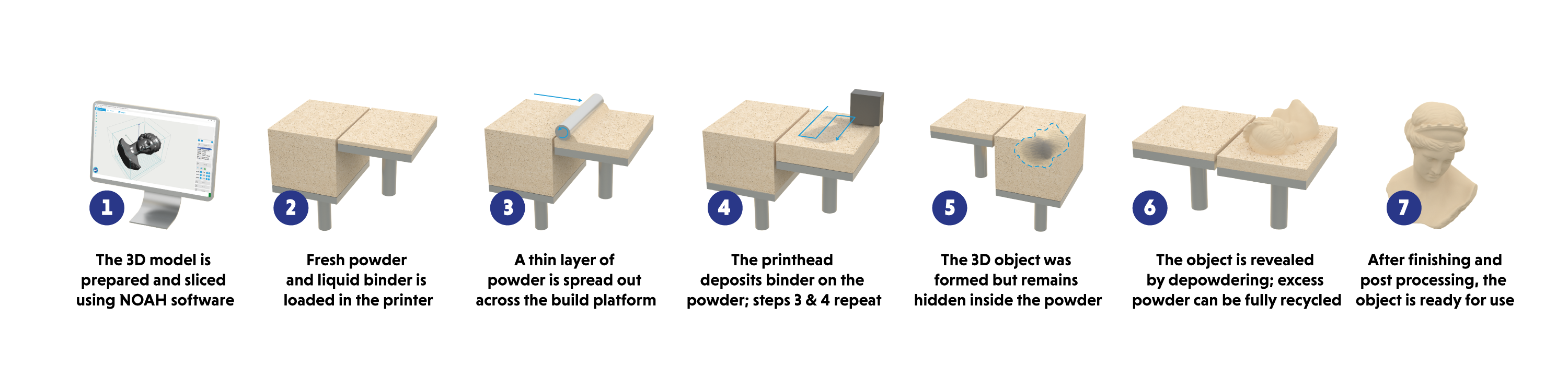
Applications of Binder Jetting
Functional Prototyping
Binder Jet 3D Printing is widely used for rapid prototyping due to its 3D Printing speed and ability to produce detailed models. Designers and engineers can quickly turn their CAD designs into physical objects, facilitating iterative testing and refinement. The technology allows for the creation of highly complex geometries and structural parts that would be difficult or impossible to achieve with traditional manufacturing methods. This makes it ideal for functional prototypes, design verification, and fit and form testing. Additionally, the ability to use a wide range of 3D Printing materials means prototypes can closely mimic the final product.
Tooling and Casting
The binder jet technology-based metal 3D Printer or Ceramic 3D Printer can used to create molds and cores for metal casting, offering a cost-effective alternative to traditional methods. Binder Jetting enables the production of highly detailed and complex Moulds that can enhance the precision and quality of cast metal parts. The process is faster and less labour-intensive than traditional mould-making techniques, reducing lead times and costs. Additionally, the ability to 3D Print moulds directly from digital designs eliminates the need for intermediate steps like pattern making. This is particularly beneficial for low-volume or custom casting jobs where traditional tooling costs would be prohibitive.
End-Use Parts
Binder Jetting is increasingly used for producing functional end-use parts, especially in industries like automotive, aerospace, and medical devices. The technology’s ability to create complex, lightweight structures with high precision is particularly valuable for aerospace and automotive applications. For example, Binder Jetting can produce intricate engine components, brackets, and heat exchangers that combine high strength with reduced weight. In the medical field, binder jet technology-based metal 3D Printer or Ceramic 3D Printer can used to manufacture custom implants, surgical instruments, and dental restorations. The ability to create parts directly from digital models enables rapid production and customization, meeting specific patient needs.
Art and Architecture
The ability to create complex and customized designs makes Binder Jetting popular in art, jewelry, and architectural modeling. Artists and designers use the technology to produce intricate sculptures, bespoke jewellery, and detailed architectural models that showcase fine details and creative geometries. Binder Jetting’s capability to work with a variety of materials, including metals, ceramics, and sands, allows for a broad range of artistic expressions and functional designs. Architectural firms leverage Binder Jetting to create accurate scale models of buildings and urban planning projects, facilitating better visualization and communication of design concepts.
Healthcare
In the medical field, Binder Jetting is used to produce customized implants, prosthetics, and surgical tools. The ability to create patient-specific 3D Printing parts from biocompatible materials enhances treatment outcomes and patient comfort. For example, Binder Jetting can produce custom bone implants that match the exact geometry of a patient’s anatomy, promoting better integration and healing. Prosthetics can be tailored to fit individual patients more comfortably and functionally. Additionally, Binder Jetting enables the production of complex surgical instruments and guides that improve the precision and efficacy of medical procedures.
Research and Development
Researchers utilize Binder Jetting 3D Printing technology for material studies and the development of new alloys and composites. The technology’s flexibility enables the rapid production of experimental models and components, allowing for iterative testing and refinement. Binder Jetting’s capability to work with a wide range of materials, including novel and experimental powders, supports advanced research in material science. Researchers can quickly produce test specimens and prototypes to study the properties and performance of new materials under various conditions. This accelerates the innovation cycle and aids in the development of advanced materials with improved characteristics.
A broad spectrum of 3D Printing materials can be used in Binder Jetting, including metals like stainless steel, copper, and titanium, which are essential for high-strength and corrosion-resistant applications. Ceramic 3D Printing with materials such as alumina and zirconia are also commonly used for their exceptional hardness and thermal resistance, making them ideal for high-temperature research. Additionally, polymers and composite materials can be utilized to explore lightweight and flexible design options. The versatility in material choice allows researchers to tailor their studies to specific application needs, from aerospace and automotive to biomedical and electronics.
Electronics
Binder Jet 3D printing technology is revolutionizing the electronics industry by enabling the production of complex and high-performance components. This technology allows for the creation of intricate electronic parts such as heat sinks, sensors, and conductive pathways, which are essential for efficient thermal management and signal transmission. The ability to print with metal powders, including copper and aluminum, provides excellent thermal and electrical conductivity, making it ideal for advanced electronic applications. Additionally, Binder Jetting supports the production of lightweight and compact components, which are crucial for miniaturized and portable electronic devices. The precision and resolution of Binder Jet 3D printing facilitate the creation of fine features and detailed structures that are difficult to achieve with traditional manufacturing methods. This flexibility accelerates the prototyping and production processes, allowing for rapid iteration and innovation in the design of electronic components. Furthermore, the technology’s capability to use a variety of 3D Printing materials, including ceramics and composites, opens up new possibilities for developing durable and high-performance electronic products. As a result, Binder Jet 3D printing is becoming an indispensable tool in the electronics industry, driving advancements and enhancing the functionality of modern electronic devices…
Future Prospects and Developments
The Binder Jetting technology is continually evolving, with ongoing research and development focused on improving material properties, surface finish, and overall performance. Advances in binding agents, powder materials, and post-processing techniques are expected to expand the applications and capabilities of Binder Jetting, making it an even more versatile and valuable additive manufacturing technology in the future.
Conclusion
Binder Jet 3D Printing is a powerful and flexible additive manufacturing process that offers unique benefits, such as high speed, material versatility, and the ability to produce complex geometries. While it has some limitations, ongoing advancements are poised to overcome these challenges, further solidifying Binder Jetting’s position in the realm of 3D printing technologies.
Industries
Industries We Serve with 3D Printing & Advanced Manufacturing
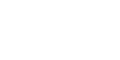
Rapid Prototyping
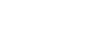
Functional Prototyping
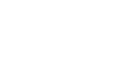
Tooling
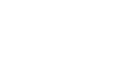
Injection Molding
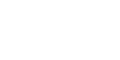
Jigs and Fixtures
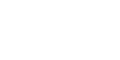
Production Parts
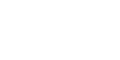
Rapid Prototyping
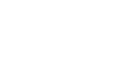
Tooling
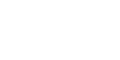
Jigs and Fixtures
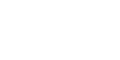
Production Parts
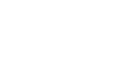
Spare Parts
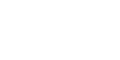
Rapid Prototyping
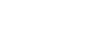
Functional Prototyping
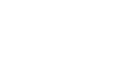
Concept/ Injection Modeling
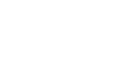
Orthodontic Models
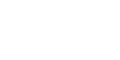
Cast Partial Frames
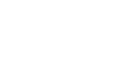
Implant Models
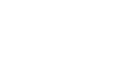
Surgical Guides
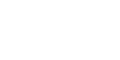
Research
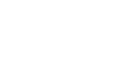
Preclinical Testing
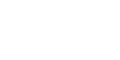
Clinical Training Models
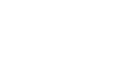
Medical Manufacturing
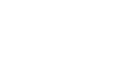